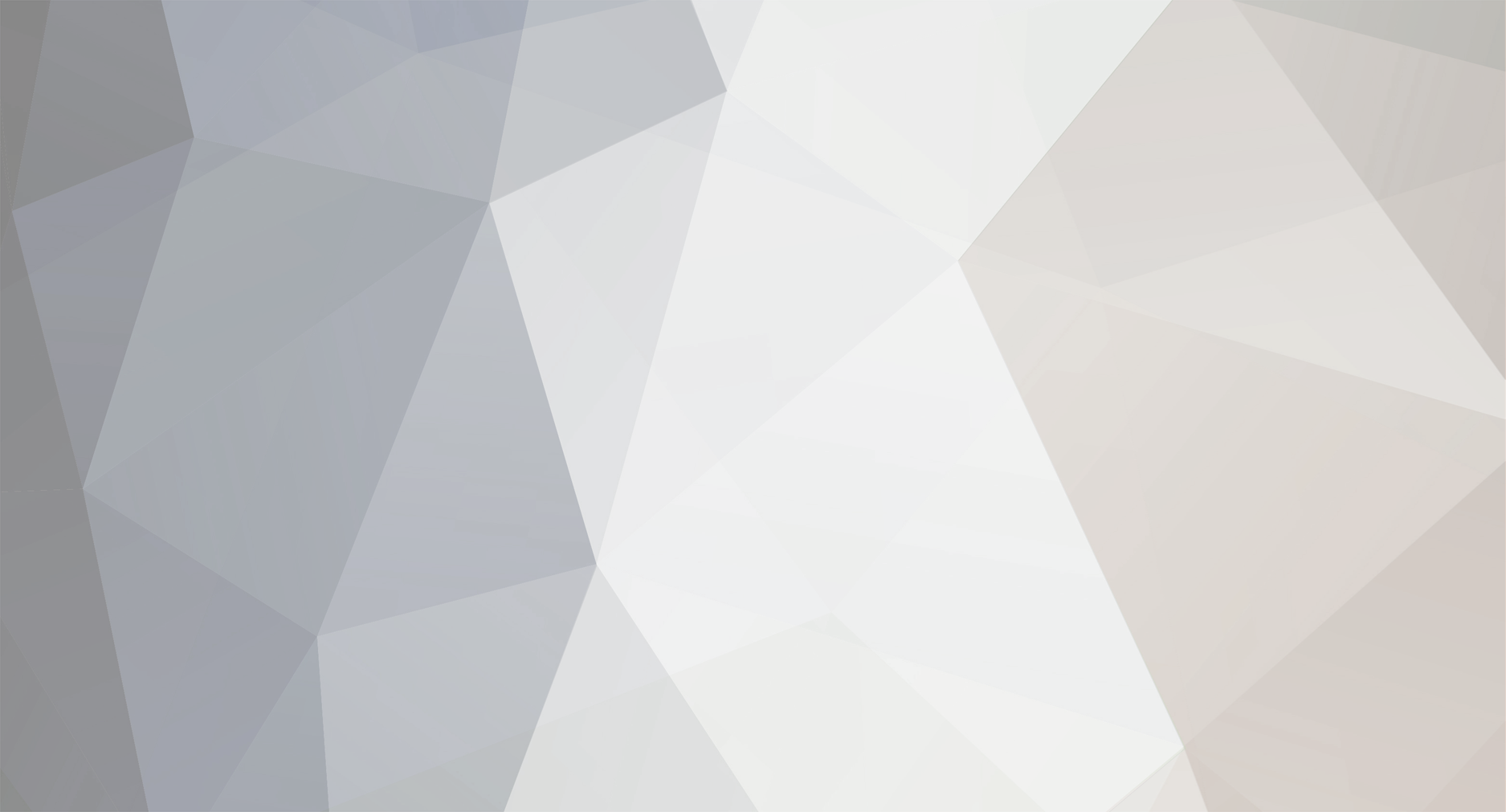
NGY
Members-
Posts
480 -
Joined
-
Days Won
20
NGY's Achievements
Newbie (1/14)
30
Reputation
-
Adding PC-Link to MDS-JE640 (like MDS-S50)
NGY replied to sfbp's topic in Technical, Tips, and Tricks
Thanks Kevin, for the invaluable input, I am sure it will be very educational for a lot of people. (And I see nothing wrong whith educated people seeking for technical perfection.) Maybe not for me, though. You could already realize, I am trying to use a "simplified" language when it comes to technical terms and explanations, for the sole reason I want it be readable for those too, who are not necessarly graduated EE-s, but still interested. I am sorry, if, for this reason (and maybe with my above work too) I look like somebody who is totally an outsider and does not know, what he was doing, just hacking left and right until gets some results by chance, and he is then so proud of this luck. No. I make serious efforts to make my posts valid, true and factual. I also did put serious work into this result above (just to pick this one as an example), regardless its Columbus's egg nature eventually (that always turns out afterwards, does not it?), and I also do have a very basic knowledge to be able to differentiate, what is allowed and what is a no-no when designing electronic devices, even if it is not reflected in my wording (that is, as I said, on purpose). You can read with a few posts above, I am keen on having all my statements based on proven facts (for example, the question of whether or not the I2C extender was a non-negligible item in a circuit like this). Matter of fact, and particulary to the point you raised, with the 100 ohm resistors I simply followed the Sony engineers, how they implemented this in another, factory stock, PC-Link enabled deck. In other words, if there had been inductances there, I would have definitely placed those instead (although none of them would be SMT devices on the keyboard pcb). The same time, I can show you another machine, when there is only a wire link there, also by design, by the Sony engineers... There are lots of examples I could also post here from Sony SM-s, but I don't feel I have to prove anything more. In the other hand though, the inductances you are (rightfully) looking for are already there on the keyboard PCB - just please take a closer look ... Please don't take this as a battle - I wanted to come up with a clean, pure solution for those who are only interested in the ultimate result to use in their machines, and even if it does not look like as a well established solution, it is thought over in all details, trust me. If you find anything you could do better (i.e., technically perfectly), then all right, but I guess not even Sony's engineers wanted to do that anyhow, so I feel totally unguilty. My solution is safe and sound. Now, with all these long posts we managed to cover dust on the main thing, for what the thread was originally created. I hope there will be just a few people who will find that post with the thing interesting and useful, and I can consider it as a little "heritage" from me, in a question that has long been unsolved (by very smart people). With that, I also want to say good bye to all these great folks here on this forum I met over the years, it is time for me to look for other adventures. MD forever. -
Such an old thread ... nevertheless, I think some people will find this piece of information interesting: the ATRAC version in the MXD-D3 is not 4.5 but actually it is Type-R. I was just about to sell my MXD-D3 the other day, then when I opened it for a last maintenance, out of sheer curiousity I pulled the drive off and turned it over. This is what I saw, to my greatest surprise: Needless to say, the D3 stayed ...
-
Adding PC-Link to MDS-JE640 (like MDS-S50)
NGY replied to sfbp's topic in Technical, Tips, and Tricks
Here is the thing then: the 640 does work now with PC-Link and M-Crew. (See my uncut, lame video at the end - "Welcome to Paradise" :-) .) Yes, it is done, and I feel this is a breakthrough, after all those unsuccessful tries in the past, including my previous attempts back in 2017 or so. The icing on the cake is the 640 has kept all its keyboard functionalities too ! I guess what you are mostly interested in is how this was made possible, and what's needed to replicate it on your machines - the shiny, polished, step-by-step guide and documentation I originally wanted to post here can wait. The beauty is that it's like Columbus' egg. Plain and simple, and all of you will now say "gosh, I should have done this easily". [I had not reinvented the wheel either, really. What I did was I took the recently purchased S50's main board I did not fear to sacrifice and began doing actual measurements of what lines/signals go where, what connections, pull-up resistors, etc. are there, and compared the thing to the SM-s. The big surprise came when I realized none of the SM-s (640, S50, PC3, etc.) tell you the true story, because this or that is different here and there, from what is on paper and what is actually on the board. Looked too complex, and I got misled quite a few times when working only from the SM-s.] I distilled all this information down to a simple, clean solution. No matter which version you have (EU, US/CAN, etc.), just follow this: [In a nutshell: there is nothing special required, everything is there already in the machine (this was my theory afterall, and it finally stood). Very minor things must be checked and supplemented, but nothing that could not be done DIY.] Check this silly drawing: These are the lines (marked with green) that must be there, all the way from the PS2 socket down to the MCU (other lines are all there, nothing to do with them). Follow these lines on your actual boards/wires one by one and see if you can get there all along. If there are jumper wires and/or 0 ohm resistors and/or inductances in series, leave them there. If you see some pull-up (typically 4k7 or 10k) and/or pull-down resistors (typically 100k) or parallel capacitors, you can also leave them all there. If the continuity breaks somewhere, look after what is missing. What must be there in order to get this working, i.e., must be supplemented in case they are missing (and normally are - see my photos with the details below): - R36 and R37 (very tiny 0 Ohm resistors) are not populated on the main board (@sfbp, you have been this close, all the rest you did well!), - two wires are missing, from CN820 on the MB up to the keyboard pcb (as seen also on @sfbp's photos), making sure you solder them in proper order (do not accidentally swap them), and - two 100 ohm resistors need to be soldered on the keyboard PCB in the positions marked "L805" and "L806" (well, plain jumper wires would also work, but in some PC-Link models these serial resistances are there, for a reason I guess). (Warning: - when measuring traces on and wires between pcb-s, don't just use your DMM directly in resistance or continuity mode. See more on this here.) - make sure you and your device are properly ESD protected, and never work on a powered up machine.) This is it, and you're done. I would love to see then the feedback from people who succesfully replicated this on their machines. - - - Next steps that now are also doable using the same approach: - for "technical maximalism": build the I2C extender circuit mentioned above (good news: the keyboard PCB is already prepared just needs to be populated, and only THT parts are required), - probably the "most wanted" one: make the 940 work like the Japanese version, PC-Link and keyboard, - a "side effect": make the keyboard work on the S50 (and on the 470 too) - similary to the I2C buffer, the MB pcb already has this area, just unpopulated, - and an "opportunity" for the low end machines: make the 440 (!) work with PC-Link and even accept a keyboard too. And some mandatory, due thanks: - @kgallen - I value your attitude for getting things done quickly (like in the case of the copybit killer stuff). This pushed me out of my "laziness". - @sfbp - your photo gave me the final "kick" that my hypothesis was right, and that I had to finish my research and do the soldering part at last. When I saw your 640's main board, I immediately realized why your attempt was unsuccessful. (And I asked for some new photos because this very part was hardly visible caused by the bright spot of the flash, but then I came across finally even without them.) - @Sony - having these features already built in (only disguised for certain markets ...) MOV01439.MPG -
Adding PC-Link to MDS-JE640 (like MDS-S50)
NGY replied to sfbp's topic in Technical, Tips, and Tricks
OK ... thanks to the "persuasion" by @kgallen , I dropped all my present tasks and spent last night and today on completing my journey. A PA will follow shortly ... stay tuned. Allow me a short break and a few hours to sleep, then I get back to you. @sfbp, don't close your 640 just yet ;-) ! -
Adding PC-Link to MDS-JE640 (like MDS-S50)
NGY replied to sfbp's topic in Technical, Tips, and Tricks
Yeah ... it is "Q34" in the 770. Funny, because both in the 640 and the 940 (and in some others) it is "Q5". -
Adding PC-Link to MDS-JE640 (like MDS-S50)
NGY replied to sfbp's topic in Technical, Tips, and Tricks
Exactly. See Q5 - this is there also to shut down the keyboard comms if and when a CAV device wants to talk to the MCU. Part of my hypotesis was that PC-Link has to have priority against the keyboard. And having Q5 there tells me - cross our fingers - the FW will "know" it once the connections part is sorted out. It certainly depends on the version of the MCU. The 640 and the family members do have separated, dedicated ports on the MCU for the I2C and the keyboard signal lines. -
Adding PC-Link to MDS-JE640 (like MDS-S50)
NGY replied to sfbp's topic in Technical, Tips, and Tricks
Exactly - I admit it is just a question of different style (me feeling uncomfortable put into writing that I could not yet finalize or could not prove beforehand). No, it is very simple, no secrets: my theory is that both from HW and FW persective everything should be already there on all three versions (1 - PC-link only, 2 - kbd only, 3 - PC-Link and kbd). However, there are differences amongst the revisions of the same board, that need to be looked after in each and every case. To give you and example - just exchanged PMs with @sfbp on this: his keyboard pcb is different from mine, and both differ from what is documented in the SM. (Also, I have information on at least three different "universal" JE640 MB boards, that seem to be the same...) Once I can confirm it with 100% certainty (I think this is what you feel "teasing", but I am simply not yet ready) what is supposed to be there on all versions in order to get this PC-Link thing going, I can move over and test whether or not the firmware supports it. There is a slight chance it will not - see the note on the different MCU versions in the S50 and the 640. It might be just an economical decision as you explained, and hopefully it is. -
Adding PC-Link to MDS-JE640 (like MDS-S50)
NGY replied to sfbp's topic in Technical, Tips, and Tricks
@kgallen, I never meant you'd stop doing your stuff as you do it very well [respect]. All I was trying to hint (from the beginning) was that there is a certain amount of work that had already been covered in the background (that could have - besides my vanity of course ;-) - saved your time), and waits only for the actual implementation. @sfbp's photos assured me I am on the right track - but of course I can still fail with it. For this, surely, if you enjoy the 'discovery', please keep going on :-) ! I will also keep my eye on this thread, and if you find something I obviously overlooked, I will take that happily. "Four eyes see more than two". -
Adding PC-Link to MDS-JE640 (like MDS-S50)
NGY replied to sfbp's topic in Technical, Tips, and Tricks
I trust you mean by "mini-DIN" the standard PS2 plug, dont' you? I never saw the PC-Link mentioned as to be used via the Contorl A1 jacks/lines. I think it is possible - to a certian extent, as the command set of the - sort of standardized - Control A1 seems limited compared to the - sort of Sony proprietary - PC-Link bus command set. EDIT: I wanted to add this note, although it might be obvious: I think the ambiguity around "PC-Link" is coming from the fact, that the deck is connected to the PC-Link device on two lines. One for the (either digital or analogue) audio transfer, and nothing else happens there, but the audio signal flow. The other line is the actual digital control of the deck, that covers controlling the deck operation (record, play, pause, etc.), transferring digital information (track/disc info, etc), as well as some editing functions, etc. The same time, the PC-Link device connects to the PC only on one line, that is the USB. It is possible to transfer audio to a non-PC-Link enabled device via the CAV box, but it lacks the control and info part (ultimately, the communication between the deck and the PC). -
Adding PC-Link to MDS-JE640 (like MDS-S50)
NGY replied to sfbp's topic in Technical, Tips, and Tricks
Looks like we are doing a "rat race" here ;-) . Even I had not posted all my steps and findings here, I feel being somewhat ahead (as been all there already, I even see now where Stephen's solution went wrong), and if you were given me some time to consolidate my knowledge and finally put into practice, we could probably lift all the clouds here at once. Yes, out of sheer vanity :-) I wanted to come up first with the ultimate solution, in a completed, polished format. But as it is just a pointless luxury that both of us are wasting precious time to discover basically the same thing :-) , maybe better approach is to wait until you also conclude with your findings, then we consolidate the stuff later. I go back to my 640 in the meantime, to do the final step. -
Adding PC-Link to MDS-JE640 (like MDS-S50)
NGY replied to sfbp's topic in Technical, Tips, and Tricks
I admire the enourmous amount of information on minidisc.org, but learned over the years that I have to take those "facts" with a grain of salt. The quote above is a bit ambiguous. Using the PC-Link, the audio signal can be transferred either via TOSLINK digital or analogue RCA. Controlling the device from a PC normally happens via the PS2 port (and the PC-Link device), but, the Control A1 has very similar commands/functionalities to that, and - in theory, I have not yet seen this documented - it can be used for the same purpose, as the PC-Link. -
Adding PC-Link to MDS-JE640 (like MDS-S50)
NGY replied to sfbp's topic in Technical, Tips, and Tricks
Good point, actually. Normally, if both functions are supported on a given (very seldom) model, then those are sharing the same PS2 port. The 470 does have a PS2 port, but on the rear panel (and w/o the keyboard functionality implemented). -
Behind the "Iron Curtain" ... Literally, but it is then sheer politics from this point, that I'd prefer to avoid on these pages. More seriously, there are two factors that would prohibit exporting such stuff to the UK for example: 1) insane shipping costs (accompanied with endless bureaucracy) of our "Royal" Post, and 2) recent impact of Brexit on import duties/taxes at the other side of the Channel. Sadly all those possible price advantages would be gone by when a box gets shipped.
-
Adding PC-Link to MDS-JE640 (like MDS-S50)
NGY replied to sfbp's topic in Technical, Tips, and Tricks
Yeah, see my addition above. So much I hate these messenger/twitter/whatsoever style posting - you cannot really think your words over, or you missed the train ... I go and take a brake break instead ... :-) -
Adding PC-Link to MDS-JE640 (like MDS-S50)
NGY replied to sfbp's topic in Technical, Tips, and Tricks
No, certainly are not, however, the I2C spec. does allow a certain length of cable, at given cable capacitance and shielding, and at a max. data rate - I am still trying to find the exact quote I noted previously, but until then: "the maximum bus length of an I2C link is about 1 meter at 100 Kbaud, or 10 meters at 10 Kbaud". So my point is (and I did drop the ball here already), that in order to get this PC-Link thing working on an otherwise not-supported deck does not depend on having this buffer or not (just keep the cable "short", and the PCLK's PS2 cable is indeed very short, I believe Sony's engineers had done their math for a reason.)